As an Amazon Associate, I earn from qualifying purchases at no extra cost to you.
Understanding Head Studs Versus Bolts in Engine Assembly?
Head studs offer better clamping force and are more reliable than bolts in engine assembly. When building an engine, understanding the differences between head studs and bolts is crucial.
Head studs provide a more uniform clamping force, creating a stronger seal and reducing the risk of head gasket failure. On the other hand, bolts can deform the threads in the engine block over time, potentially leading to leaks or other issues.
By choosing the right fastener for your engine, you can enhance performance and reliability. Let’s delve deeper into the significance of head studs versus bolts in engine assembly to make an informed decision for your next build.
What Are Head Studs And Bolts?
The proper fastening of the cylinder heads to the engine block is vital for an engine’s performance and reliability. Head studs and head bolts are the two primary methods used for this purpose. Understanding the differences between these two fastening techniques is critical for engine builders and tuners. In this section, we will explore the meanings, functions, and differences of head studs and head bolts in engine assembly.
Head Studs
Head studs are threaded rods, typically made of a high-strength alloy steel, that are inserted into the engine block to secure the cylinder head. This type of fastener is designed to provide a consistent clamping force and better load distribution compared to head bolts. The use of head studs is prevalent in high-performance and racing engines due to their superior strength and reliability.
Head Bolts
Head bolts are one-piece fasteners that are threaded on both ends. They are commonly used to secure the cylinder head to the engine block in most production vehicles. Head bolts rely on torque to provide clamping force, which can lead to uneven pressure distribution. However, advancements in head bolt design have improved their performance, making them suitable for many engines.
Advantages Of Head Studs
Head studs offer several advantages over bolts in engine assembly, providing higher clamping force, improved cylinder head alignment, and better stress distribution.
Higher Clamping Force
- Studs provide consistent and stronger clamping, reducing the risk of head gasket failure.
- Increased clamping force helps maintain a tight seal for optimal engine performance.
Improved Cylinder Head Alignment
- Studs facilitate precise positioning of the cylinder head for perfect alignment.
- Proper alignment enhances engine efficiency and reduces wear on components.
Better Stress Distribution
- Studs evenly distribute stress across the cylinder head, preventing localized pressure points.
- Uniform stress distribution improves the longevity and reliability of the engine assembly.
Advantages Of Head Bolts
When it comes to engine assembly, understanding the difference between head studs and bolts is crucial. Let’s focus on the advantages of head bolts in this comparison.
Ease Of Installation
Head bolts offer simple installation process making them suitable for beginners. They require basic tools and are easier to manage during assembly.
Cost-effectiveness
Head bolts are more affordable compared to studs, making them a cost-effective option for engine assembly. They provide reliable performance without breaking the bank.
Availability
Head bolts are readily available in most automotive stores, ensuring easy access for anyone undertaking an engine assembly project. Their widespread availability makes them a convenient choice.
Applications For Head Studs
When it comes to assembling an engine, understanding the importance of head studs versus bolts is crucial. In this section, we will delve into the various applications for head studs, particularly in high-performance engines and the forces acting on the cylinder head. Proper installation of head studs is essential for maintaining the integrity of the engine’s assembly.
High-performance Engines
High-performance engines, such as those used in racing or high-output applications, often require head studs due to the increased stress and thermal expansion. Head studs provide superior clamping force and uniformity, reducing the risk of head gasket failure in high-boost or high-compression setups.
Forces On Cylinder Head
The forces acting on the cylinder head in an engine are significant, particularly in high-performance and forced-induction applications. The combustion pressures and thermal expansion can exert immense force on the cylinder head. Head studs effectively distribute these forces, helping to maintain the head gasket seal and preventing head lift under extreme conditions.
Applications For Head Bolts
When it comes to engine assembly, choosing the right fasteners is crucial for optimal performance and reliability. Head bolts play a significant role in keeping the cylinder head securely in place on the engine block. Understanding the applications for head bolts is essential for ensuring proper engine function and avoiding potential problems down the road.
Standard Engines
Standard engines typically utilize head bolts as the preferred fastening method for securing the cylinder head. These bolts are designed to provide a strong and reliable connection between the cylinder head and the engine block. They can withstand the high pressures and heat generated during engine operation, ensuring the cylinder head remains firmly in place.
Head bolts for standard engines are usually made of high-quality steel, which offers the necessary strength and durability to handle the demands of a typical engine. These bolts are precisely engineered to provide the correct clamping force, preventing any movement or leakage between the cylinder head and the engine block.
Low-stress Applications
In certain low-stress applications, head bolts might be a suitable choice. These applications involve engines that operate under minimal stress or conditions where the engine is not subjected to extreme temperatures or high-performance demands. Examples of low-stress applications include small motorcycles, lawnmowers, and simple consumer-grade engines.
Using head bolts in low-stress applications can simplify the assembly process, as these bolts are often easier to install and remove compared to head studs. However, it’s important to note that using head bolts in high-performance or demanding applications can lead to potential issues, such as head gasket failure or cylinder head warping.
When selecting head bolts for low-stress applications, it’s crucial to ensure they meet the manufacturer’s specifications and are suitable for the engine’s requirements. Using improper head bolts can compromise engine performance and reliability, leading to costly repairs.
Summary
Understanding the applications for head bolts is essential in engine assembly. For standard engines, head bolts are the preferred choice due to their strength and ability to handle high pressures and heat. However, in low-stress applications, head bolts can be used as a simpler alternative. Regardless of the application, it’s vital to select the correct type and quality of head bolts to ensure optimal engine function and longevity.
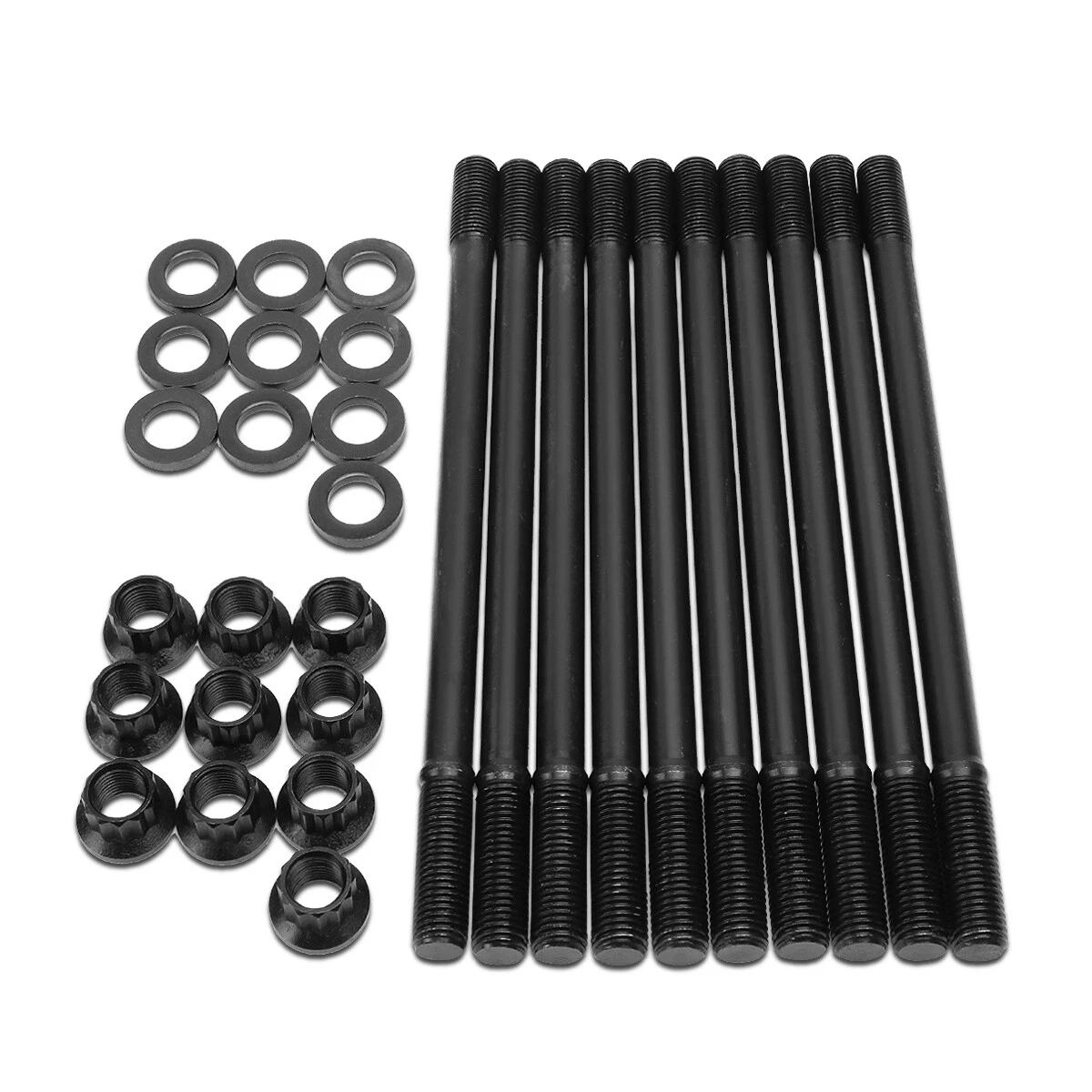
Credit: www.ebay.com
Factors To Consider
When it comes to engine assembly, choosing between head studs and bolts is an important decision. Both options have their advantages and disadvantages, and making the right choice depends on several factors. Here are three key considerations to keep in mind:
The type of engine you have and your performance goals play a significant role in determining whether to use head studs or bolts in the assembly process. Head studs are known for their superior clamping force and ability to handle extreme power levels, making them ideal for high-performance engines. On the other hand, head bolts are more commonly used in stock or mildly modified engines. If you have a race car or a heavily modified engine, head studs may be the better choice.
When it comes to budget and availability, head studs tend to be more expensive than head bolts. This is mainly due to the fact that head studs are made from higher-grade materials and offer better performance. Additionally, head studs are not as widely available as head bolts, especially for less popular engine models. However, if your budget allows for it and you can find the necessary head studs for your engine, they can provide greater peace of mind and long-term durability.
Your experience with engine assembly is another crucial factor to consider. If you’re a seasoned mechanic or have experience working with engines, using head studs may not pose any challenges for you. However, if you’re new to engine assembly or have limited experience, head bolts may be the easier option. Head bolts are generally simpler to install and require less expertise. It’s crucial to ensure that the assembly is done correctly, regardless of which option you choose, to avoid any potential issues down the line.
Choosing The Right Fastener
When it comes to engine assembly, selecting the right fastener is crucial. Understanding the difference between head studs and bolts is essential to ensure the proper strength and performance of an engine. Let's explore the key factors to consider when choosing the right fastener for your engine assembly.
Weight Considerations
The weight of the fastener plays a significant role in engine assembly. Head studs are generally lighter than bolts, which can contribute to reducing the overall weight of the engine. This weight reduction can enhance the engine’s performance and fuel efficiency, making it a favorable choice for performance-oriented applications. On the other hand, bolts may add more weight due to their design, making them suitable for applications where added weight isn’t a concern.
Maintenance And Future Repairs
Consider the maintenance and future repair aspects when deciding between head studs and bolts. Head studs are known for their ease of maintenance and future repairs. In scenarios where the cylinder head needs to be removed frequently, such as in high-performance applications, head studs provide convenient access and reusability. However, bolts can also be suitable for engines that require less frequent maintenance and repairs, depending on the specific application and maintenance schedule.
Professional Recommendations
Seeking professional recommendations is essential when making a decision about head studs versus bolts for engine assembly. Consulting with experienced engine builders and professional technicians can provide valuable insights based on the specific engine application, performance goals, and maintenance requirements. Their expertise can guide you in selecting the optimal fastener type that aligns with your engine’s needs, ensuring reliability and performance.
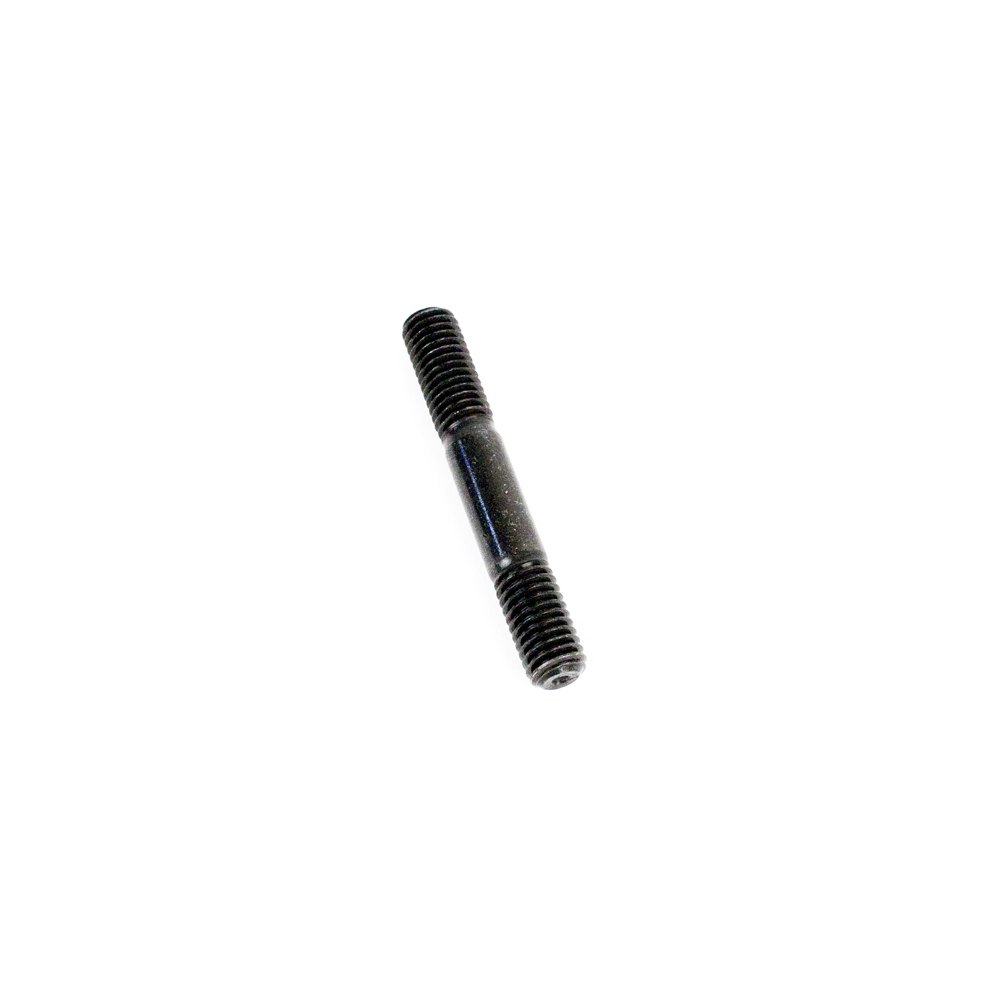
Credit: cometkartsales.com
Installation Tips
When installing head studs or bolts in engine assembly, following proper procedures is crucial to ensure a secure and reliable connection.
Proper Torque Specifications
– Refer to the manufacturer’s specifications for the correct torque value.
– Using a quality torque wrench, apply torque gradually and uniformly in multiple steps.
– Never exceed the recommended torque to avoid damaging the components.
Use Of Thread Sealant
– Apply a suitable thread sealant to prevent oil or coolant leaks.
– Ensure the sealant is compatible with the material of the studs or bolts.
– Follow the curing time recommended by the manufacturer before torquing.
Retorque Procedure
– After initial installation, recheck the torque after the engine has gone through a heat cycle.
– Follow the specific retorque sequence provided by the manufacturer.
– Periodically check and retorque the studs/bolts to maintain proper clamping force.

Credit: www.ebay.com
Conclusion
Choosing between head studs and bolts is crucial for engine performance and reliability. While bolts provide convenience and are cost-effective, head studs offer superior strength and stability. Ultimately, the decision rests on the specific requirements of your engine and your budget.
By understanding the differences, you can make an informed choice for your engine assembly needs.