As an Amazon Associate, I earn from qualifying purchases at no extra cost to you.
What’s the Proper Torque for LS Rocker Arms? The Ultimate Guide
If you're diving into the world of LS engines, then you're probably aware that there are a lot of things to consider when you’re building or working on one. But one of the most crucial details often gets overlooked – the proper torque for LS rocker arms. Trust me, getting the torque right is essential to ensure your engine runs smoothly and efficiently. But don’t worry – this guide will walk you through everything you need to know in a way that's super easy to follow. Whether you’re a seasoned mechanic or just someone tinkering with your first LS engine, we've got you covered. Let’s dig into this!
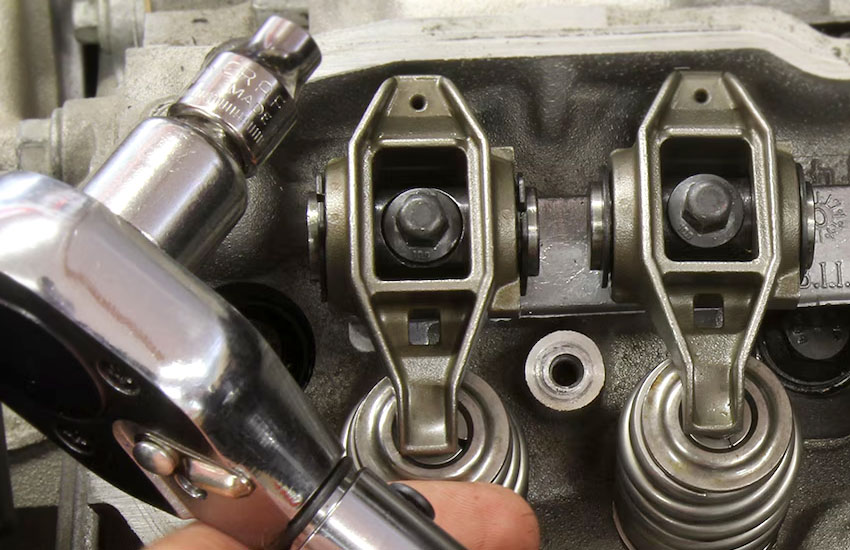
Understanding the Importance of Proper Torque for LS Rocker Arms
When you’re dealing with an LS engine, every little detail matters, and the torque on the rocker arms is no exception. You might be wondering, why is the torque so important? Well, torque is essentially the force that ensures all the parts in your engine are snug and working together properly. Too much torque, and you risk damaging the components. Too little torque, and you might end up with parts that are loose or underperforming. For rocker arms, which play a critical role in controlling the opening and closing of your engine’s valves, having the correct torque ensures they function optimally.
So, what is the proper torque for LS rocker arms? It's a bit more complicated than just one answer, as it depends on the specific setup you’re using. That's why understanding the fundamentals and how to apply the right torque is key to getting the best performance out of your engine.
Why Torque Matters for Rocker Arms
The rocker arms are part of your engine's valvetrain system, and they control the timing of your engine's intake and exhaust valves. These components experience constant pressure and heat, making it essential to secure them properly with the correct torque. Too much torque can damage the threads on the bolts or warp the rocker arms themselves. Too little torque and they could come loose, causing major engine problems.
Ensuring that each rocker arm is installed with the proper torque helps maintain consistent valve timing, reducing the risk of misfires, power loss, or even engine failure. That's why understanding how much torque is needed for your specific LS engine setup is crucial for its longevity and performance.
How to Determine the Proper Torque for LS Rocker Arms
Determining the proper torque for LS rocker arms depends on the type of rocker arms you're using and the specifications from the manufacturer. Typically, LS rocker arms are torqued using a specific torque setting, often ranging from 22 to 30 foot-pounds (ft-lb). But that's just a general guideline – each setup could require something slightly different.
LS Engine Types and Their Torque Specifications
LS engines come in different configurations, and each type can have its own torque specs. For example, the popular LS1, LS2, and LS3 engines may have different torque specifications based on the year, model, and specific performance goals. Always consult the service manual or the manufacturer's recommendations for the exact torque settings for your engine's rocker arms.
For stock LS rocker arms, the torque typically falls around the 22-30 ft-lb range, but for performance setups, like those with aftermarket rocker arms or high-performance camshafts, the torque may be slightly different. So, while it's always best to go with the manufacturer's recommendation, understanding the general torque range is a good starting point.
How to Torque LS Rocker Arms Correctly
Once you know the proper torque setting for your LS rocker arms, it's time to put that knowledge into action. Here's a step-by-step guide on how to torque your rocker arms correctly:
- Gather the Necessary Tools: Before you get started, make sure you have the proper tools. You'll need a torque wrench, a socket wrench, and the correct socket size for your rocker arm bolts.
- Check Your Torque Settings: As mentioned, you'll need to check the torque specifications for your specific LS engine. These specs are usually provided in the engine's service manual or by the manufacturer of the rocker arms.
- Tighten in the Correct Sequence: When torquing the rocker arms, it's essential to follow the correct sequence to ensure even pressure. Start with the middle bolts and work your way out, tightening in a criss-cross pattern.
- Torque in Stages: To avoid over-tightening or under-tightening, torque the bolts in stages. Start by tightening to about half of the final torque specification, then go over it a second time to reach the final setting.
- Double-Check: After you've torqued all the bolts, it's always a good idea to go over them again to ensure they're all properly tightened.
Following these steps will ensure that your LS rocker arms are torqued correctly, which will, in turn, keep your engine running smoothly.
The Tools You Need to Torque LS Rocker Arms Properly
Now that you know the importance of the correct torque and how to apply it, let's talk about the tools you’ll need. Having the right tools is essential for achieving the perfect torque without risking damage to your engine. Let's break down the tools you'll need.
Torque Wrench
The most important tool when torquing LS rocker arms is a good quality torque wrench. A torque wrench allows you to apply the exact amount of torque to each bolt, ensuring that you don't over-tighten or under-tighten them. There are two main types of torque wrenches: click-style and beam-style. Click-style wrenches are more precise and easier to use, while beam-style wrenches are more affordable but less accurate.
Socket Set
In addition to a torque wrench, you'll need a socket set that fits the bolts on your rocker arms. For LS engines, the bolt size will typically be either 7/16-inch or 1/2-inch, depending on your setup. It's important to have the right size socket to ensure a secure grip on the bolt.
Ratchet Wrench
A ratchet wrench will make it easier to tighten the bolts to a snug fit before using the torque wrench. It's also useful for loosening the bolts if you need to make adjustments during the process.
Extension Bar (Optional)
Sometimes, you may need an extension bar to reach the bolts if they're located in hard-to-reach areas. This tool isn't always necessary, but it can make your job a lot easier if you're working in tight spaces.
Common Mistakes to Avoid When Torquing LS Rocker Arms
Even though torqueing LS rocker arms seems straightforward, many DIY enthusiasts and even seasoned mechanics make mistakes during the process. Let's go over some of the most common mistakes so you can avoid them.
Over-tightening or Under-tightening
One of the most common mistakes is either over-tightening or under-tightening the bolts. Over-tightening can strip the threads, warp the rocker arms, or damage the bolts. On the other hand, under-tightening can cause the bolts to come loose, leading to misfires or engine damage. Always use a torque wrench and double-check the manufacturer's recommended torque settings.
Using the Wrong Torque Wrench
Not all torque wrenches are created equal. Some are more accurate than others. If you use a low-quality or inaccurate torque wrench, you risk not applying the proper torque to your rocker arm bolts. It's best to invest in a good quality torque wrench for the most accurate results.
Incorrect Torque Sequence
Another common mistake is not following the correct torque sequence. If you don't torque the rocker arms in the proper order, the pressure could be uneven, potentially causing damage to the rocker arms or the cylinder heads. Make sure to follow the correct pattern for torquing the bolts.
Forgetting to Recheck Torque
After you've torqued all the rocker arm bolts, it's always a good idea to recheck them after a few runs. Sometimes, bolts can loosen up over time, especially after an engine has been running for a while. Rechecking your torque will help ensure everything stays secure.
Frequently Asked Questions
Is it safe to torque LS rocker arms by hand?
No, it's important to use a torque wrench to apply the correct torque. Doing it by hand can lead to over-tightening or under-tightening.
Can I reuse the rocker arm bolts after removing them?
While it's possible to reuse the bolts, it's always a good idea to inspect them for wear and tear. If they're damaged, replace them with new ones to ensure the best performance.
Do I need a special torque wrench for LS engines?
No, any high-quality torque wrench that covers the torque range of 22-30 ft-lb should work fine for LS engines. However, ensure it's accurate for the best results.
Is it normal for LS rocker arms to make noise after installation?
Some noise can be expected, especially if the engine is breaking in. However, excessive noise may indicate an issue with the torque or rocker arm installation.
Can I torque the rocker arms too many times?
Yes, repeated torquing can damage the bolts or threads, so always make sure to torque the bolts properly the first time.
Is there a torque setting for aftermarket rocker arms?
Yes, aftermarket rocker arms may have different torque specifications. Always refer to the manufacturer's instructions for the proper torque.
Do I need to use a lubricant on the rocker arm bolts?
Using a small amount of lubricant or threadlocker can help prevent seizing, but be sure to follow the manufacturer's recommendations.
Is it necessary to replace the rocker arm bolts every time I remove them?
It's not always necessary, but it's often recommended to replace rocker arm bolts every time they are removed to ensure a secure fit.
I hope this guide helps you understand the importance of proper torque for LS rocker arms and how to do it right. By following the steps outlined above, you can ensure that your engine runs smoothly and efficiently, without risking damage to your valuable components. Remember to always follow the manufacturer's recommendations, and if in doubt, don't hesitate to consult a professional. Happy building!